
adsorbent to clean associated petroleum gas from hydrogen sulfide

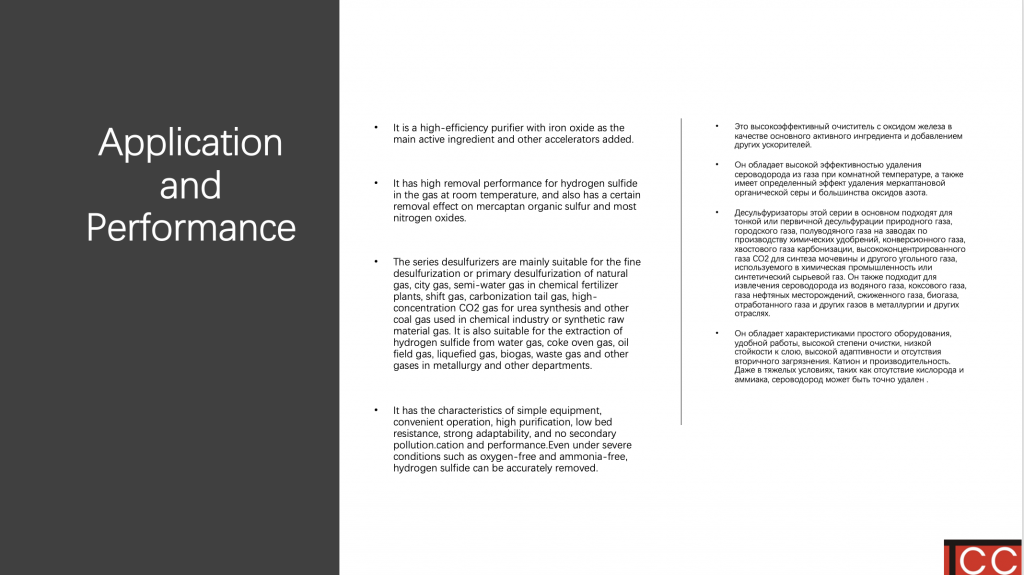
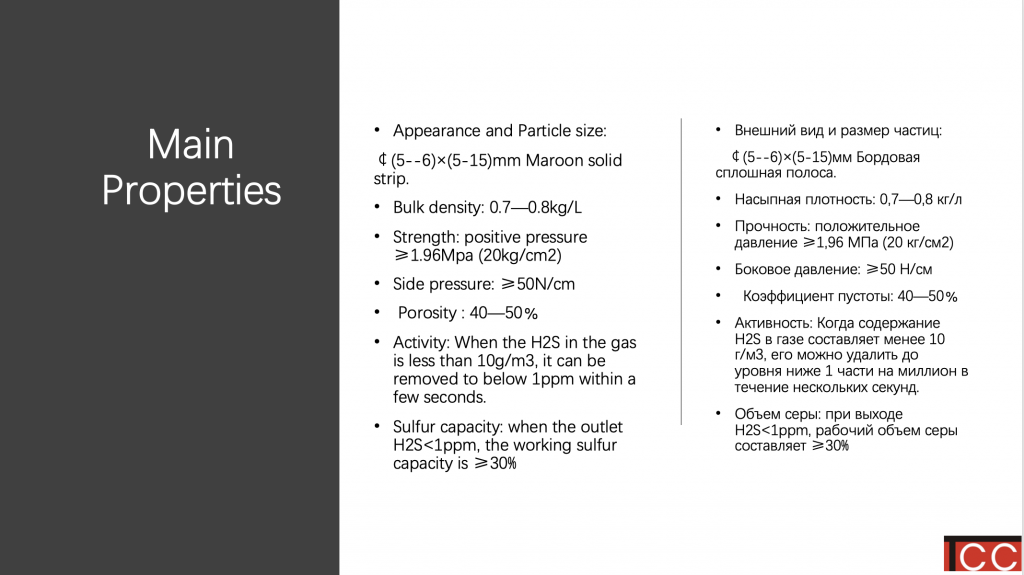
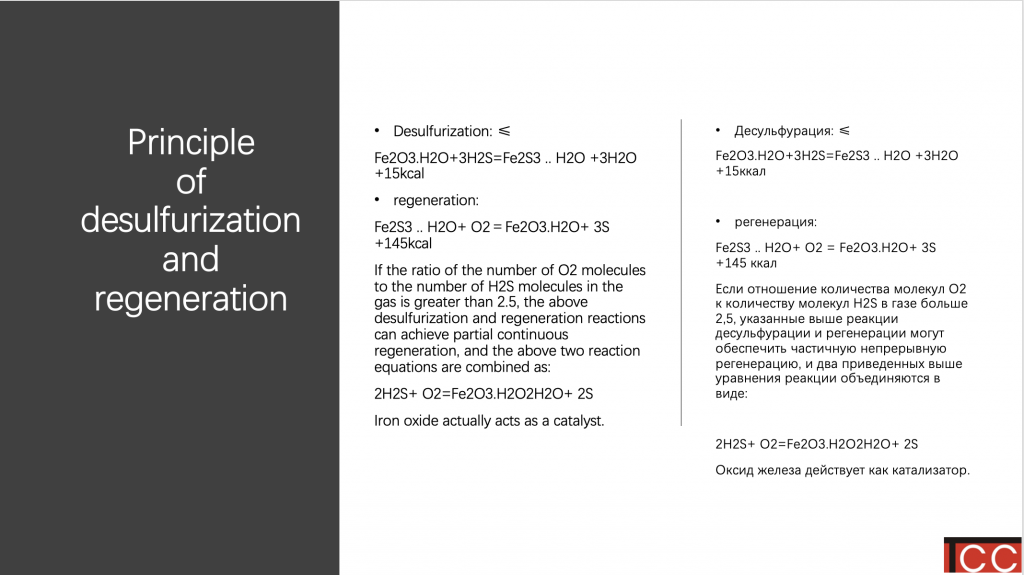
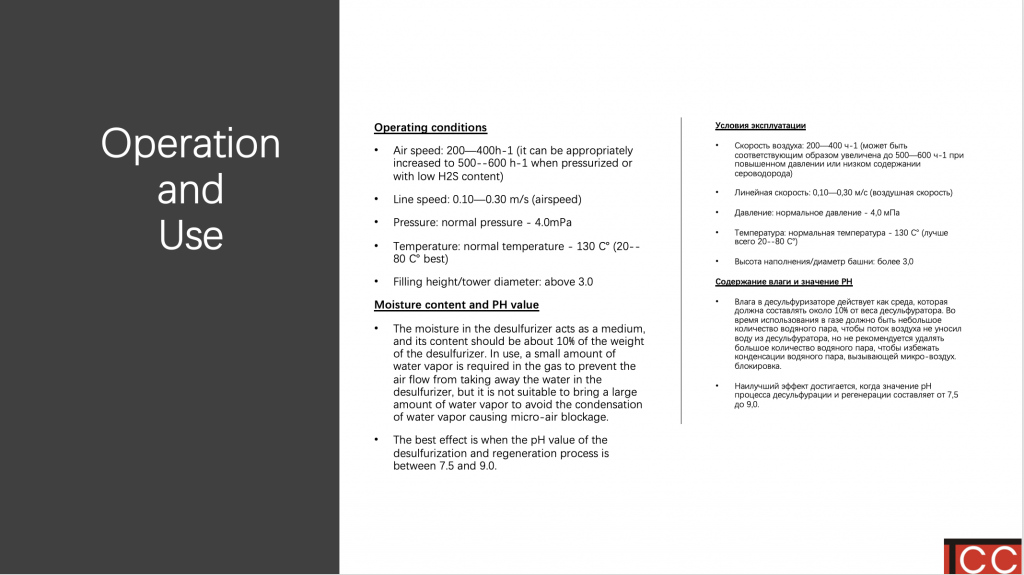
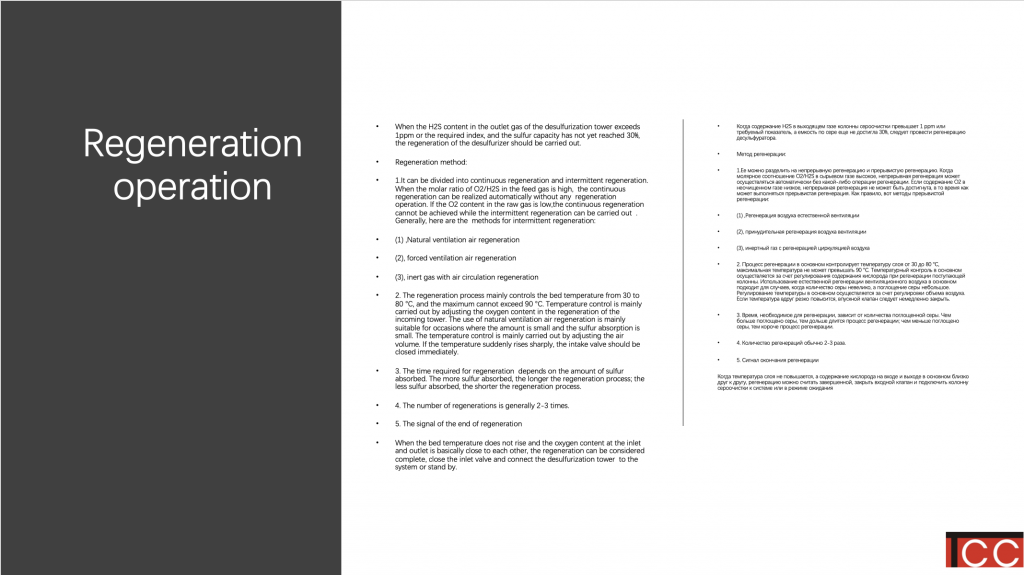
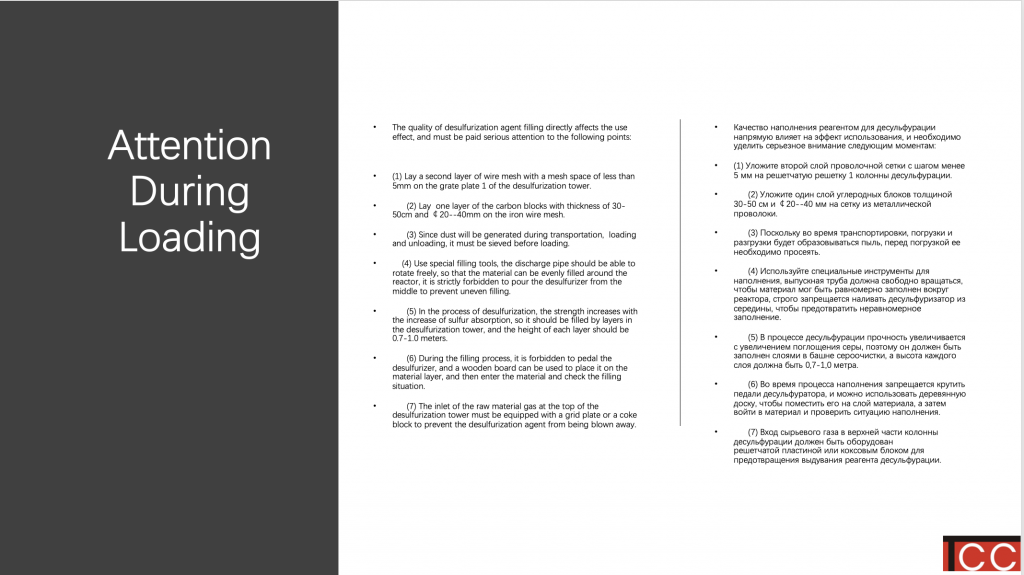
The most cost-effective for the small metal parts which are less than 50g.
For some small metal parts which are less than 50gram, they used to be casted directly in the past. Since there is another process called metal injection molding which is focusing on the small parts in recently years, which process is the most cost effective way?
Mostly the MIM is more suitable than the investment casting, however, It still need to be analyzed case by case.
Let’s take the wear segment like above image as an example.
The weight is 36 Grams.
The structure of this part is simple.
The dispatch condition is blank casting or raw part.
The tolerance is referred to VDG-Sheet P690 D1
The annual quantity for this part is around 30,000/ year.
According to this information, It is concluded that the investment casting is most cost- effective process to manufacture this part. For the molding cost of this part , metal injection molding(MIM) is three times than the investment casting.For the unit cost of this part, Metal injection molding is 2.5 times than the investment casting.
The advantages of metal injection molding compare to investment casting are follows.
So you can see none of these advantages are applied on this part .
If you have some small parts to OEMs, let’s discuss case by case and we will give you the best solution. Please send email to alina@tcc-casting.com
Aerospace Investment Castings
When aeronautical engineers design aircraft ,considering the safe, perform well, and can be built and sold at a competitive price, for certain parts with unusual or complicated shapes it is often by casting with appropriate heat treating and machining rather than forging .Investment casting is more economically and technically feasible on aerospace industry.Parts ranging from high to low complexity which are made from durable and corrosion resistant materials are possible. TCC understand the quality and precision that the industry demands which enable us to provide a wide range of investment cast parts for applications in both commercial and military aerospace sectors.
At TCC, we have a proven track record of producing some investment cast parts for aerospace applications that meet strict industry standards , eg bracket for J-10CE. Some of our capabilities in this sector are as follow:
In depth knowledge in working with a vast number of standard and super alloys such as stainless steel, PH stainless steels (17-4 ), carbon steel, and Nickel based super alloys like Inconel 718, Inconel 625, and alluminum alloy.
Use of the latest 3D modeling (SolidWorks) and solidification analysis (Pro-Cast) software’s.
In house rapid prototyping technologies with the ability to print 3D waxes.
When necessary we can design and implement soluble and ceramic cores into our tooling and workflow.
With a high level of casting expertise, stringent process control and certified quality systems of AS9001, we proudly provide reliable and cost-effective aerospace investment castings for the following applications:
Valves
Mounts
Swirl Nozzles
Engine Blades
Engine Rings
Vanes
Engine Impellers
Aircraft fluid management systems
Interior components
Hydraulic fluid system components
Quality is always the top priority at TCC. Certifications and compliances we adhere to for the aerospace industry is EN ISO 9001:2015 and EN9100:2018 .
For more details , please contact us with email : alina@tcc-casting.com
turn-key supply
Experience achieved flare and power burner parts for combustion system OEMs in the Oil & Gas industry, TCC now has not only manufacture the spare parts and the tube ,but the flare tips design and assemble , such as the spare and replacement of gas tips, flame stabilizers (cones or diffusers), ignition components, burner pilot parts . All components in the heat-affected zone are made from 310 stainless steel (HK) material and some others are made of AISI304 .
Our gas tips are engineered and manufactured to strict tolerances to meet client’s equipment functions pOur gas tips are engineered and manufactured with strict tolerances to meet client’s equipment functions properly. Our cones, flame stabilizers, and pressure block devices are cast or manufactured from high-grade materials to ensure long life and performance.TCC can supply a wide variety of investment cast or fabricated cones / flame holders / diffusers for round or flat flame burners.
Contact us for more technic information through email alina@tcc-casting.com.
Metal injection molding for small connector
Metal injection molding is a metalworking process in which finely-powdered metal is mixed with binder material to produce a “feedstock” which is then shaped by injection molding.
The complex parts just need to be shaped in one step during the whole process. After molding, the part undergoes conditioning operations to remove the binder and densify the powder.
As the good performance on roughness , tolerance ,high efficiency than other technic .The metal injection molding market has grown quickly , especially some fields, eg,consumer electronics and IT sectors, medical and orthodontic fields and automotive industry.
The demand for small, sophisticated, high-volume components has made MIM thriving in the electronics area.
Connectors with complex geometries are now the main MIM products, and the miniaturization of electronic devices requires smaller components to achieve better performance at lower cost. This is where metal injection molding can take advantage of it.
Metal injection molding is used to produce lightning connectors for smartphone devices, which are tens of millions produced per week at peak production. This small, complex component with high-volume can be produced in multi-cavity molds to net-shape. Few other technologies can be compared with high volume capacity and tight tolerances of metal injection molding.
If you have some small parts need to design , from the material to the structure , our technician can design the good cost performance product for you .please contact us by email alina@tcc-casting.com
Investment casting for boiler accessories and combustion parts
The commonly casting material for boiler accessories and combustion parts is heat-resistant steel, the widely used is HH, HK, A-27 GR60-30 and CL1/ G17CrMO5-5. The common casting methods are silica sol investment casting and sand casting. For the investment casting , The weight can be casted from 0.01g to 120kg with the tolerance CT5 to CT7 and the surface roughness from Ra 3.2 to 12.5. For the sand casting , The weight can be casted from 5kg to 2500kg with the tolerance CT11 to CT13 and the surface roughness from Ra 25 to 50.
Technic | Material | Weight | Tolerance | Roughness |
Silica sol investment casting | HH,HK,A-27 GR60-30, CL1/G17CrMo5-5 | 0.01-120KG | CT5-CT7 | Ra3.2-12.5 |
Sand casting | HH,HK,A-27 GR60-30, CL1/G17CrMo5-5 | 5-2500KG | CT11-CT13 | Ra25-50 |
The Common boiler accessories are hood, such as double hole arrow hood, porous cap, grille hood, “7” type hood, and support block, sliding block, male and female buckle, grate hanging plate, pipe clamp, anti-wearing tile and so on
TCC is experienced in manufacturing the boiler accessories and combustion parts .If you have any inquiry , our technician are happy to discuss with you , please feel free to contact email alina@tcc-casting.com
Where MIM Differs from PM?
It is usually confused MIM with traditional press-sinter powder metallurgy (PM). The standard powder metallurgy forming step relies on vertical axis compaction to press a coarse powder into compact. The pressing route is the same as used to form pharmaceuticals pills. Die compaction is best at forming squat shapes that are easily ejected from the tooling while the ejection step requires the sides be parallel, a restriction in geometry not seen in MIM.
The major difference in the two technologies is in the final density and final properties. Because of friction between the powder and tooling, pressed powder is non-uniform. If sintered in a high temperature like MIM sintering cycle, the component would warp, like a potato chip. Thus, PM parts are lightly sintered and retain considerable porosity and have significant property degradations.
For PM , it uses larger powders versus MIM and to sinter at lower temperatures for shorter times to avoid distortion during sintering densification, resulting in lower properties. As an example, MIM strengths are about two-fold higher than PM, fatigue strength is more three-fold that of PM, and impact toughness is eight-fold higher when compared to PM.
Where Does MIM Fit?
Considering saving cost , PM may be a cost-effective alternative for simple parts while MIM can produce parts with complicated geometries to eliminate secondary operations when it comes to high-density, high-complexity components that cannot be made by any other manufacturing process ,
Additional savings are found when you consider materials, design, assembly and logistic benefits to the MIM process, especial when the two or more subcomponents made by other production processes are combined into one single MIM component.
On every project, we aim to deliver more consistent parts, more efficiently, at lower costs. We discuss with customer and decide the material , change the design to reduce the weight ,revise the drawing to do away with the expenses associated with secondary processes such as machining, achieving net-shape in one time.
If you have such inquiry , our technician will be glad to discuss with you . Feel free to contact us and send email by alina@tcc-casting.com
Which way has the better cost performance?
One inquiry recently from our customer to ask quote by investment casting technique. According to the drawing, the material of this part is 1.4409 and the weight is 30gr, 15000pcs/batch. After our analyzing , metal powder injection molding is better than silica sol investment casting. Here is the reason below.
-The weight which is not more than 50 gr , it is fit for MIM.
– 316L of MIM is the equivalent material for 1.4409 .
-The more quantities, the higher cost performance for MIM.
– MIM has much more better surface roughness and tolerance than silica sol Investment casting . For MIM, the tolerance of is a 0.3% to 0.5% and the surface roughness is Ra 0.8 to Ra1.6 while the tolerance is CT4 to CT6 and the surface roughness is Ra 3.2 to Ra 6.3 for silica sol investment casting. Less machining of MIM has to be done.
If you have some parts with the below conditions. MIM could be considered priority.
-The weight of the parts is better more than 0.2g and no more than 50g .
-The Wall thickness of the part is above 0.5mm.
-Complicated structure or shape for the part.
-Higher requirement for the surface roughness and the tolerance.
– quantities better 10,000pcs.
For more details if the part has the right technic , please contact us to discuss further. our email address is alina@tcc-casting.com
GX5CrNi19-10 (EN 1.4308) is same stainless steel material as SS304, EN 10213: 2007 Steel castings for pressure purposes EN 10283: 2010 Corrosion resistant steel castings ISO 11972:2015 specifies cast steels for general corrosion-resistant applications.X5CrNi18-10 (EN 1.4301) is the similar grade in standard of in EN 10088-3
GX5CrNi19-10 (EN 1.4308) similar grade:
American: ASTM A351 CF8 (J92600)
American: ASTM A743 CF8 (J92600)
American: ASTM A744 CF8 (J92600)
American: ASTM A297 CF8 (J92600)
Japanese: JIS 5151 SCS13
Chinese: GB/T 12230 ZG0Cr18Ni9
France: AFNOR Z6CN18.10M; Z6CN19.9M
UK: BS3100-4 304C15
Korea: KS D4103 SCS13
Germany: DIN 17445 GX6CrNi18-9
Heat to 1050-1150°C for sufficient time to heat casting uniformly to temperature and water quench
Corrosion and pitting resistance Better for abrasive applications
Higher strength than standard stainless steel Improved ductility and weldability
Better resistance to embrittlement
it’s the most popular stainless steel used in such Pump industry, Machinery spare part ,Automobile industry , Food industry…
If you have some parts which could be machining directly or cast , let’s discuss what kind of technic is most fit for you . TCC’s technician could design the drawing for you according to your idea , or propose the most suitable technic for you . Contact TCC casting .
Gravity Die Casting VS Pressure Die Casting
There are two main processes which is gravity die casting and pressure die casting for Aluminum alloy .
Gravity Die Casting ( called Permanent Mold Casting in USA and Canada)is a permanent mold casting process , where the molten metal is poured from a vessel or ladle into the mold. The mold cavity fills with no force other than gravity, filling can be controlled by tilting the die. Undercuts, and cavities can be incorporated into the component form with the use of sand cores.
It specifically refers to metal casting, however, sand casting, metal casting, investment casting, lost mold casting can also be included generally .
Advantages of Gravity Die casting
-Less pores and can be heat treated.
-Low density
-Product finish is not high.
-Low production efficiency.
-Molding with long lifetime and low cost
-Simple technic process
-Not suitable for parts with thinner wall.
Pressure Die casting includes high pressure casting and low pressure casting.
Low-pressure die casting is a method of production that uses pressure – rather than gravity – to fill molds with molten metal such as aluminum and magnesium. In this process, the holding furnace is located below the cast and the liquid metal is forced upwards through a riser tube and into the cavity. The pressure is applied constantly, sometimes in increasing increments, to fill the mold and hold the metal in place within the die until it solidifies. Once the cast has solidified, the pressure is released and any residual liquid in the tube or cavity flows back into the holding furnace for “recycling.” When cooled, the cast is simply removed.
Advantages of Low-Pressure Die Casting
-Precise control of the filling process.
-Reduces oxide formation and porosity.
-Ensure superior consistency of the partsfrom top to bottom
-Exceptional density , strength values and excellent dimensional accuracy.
-Fit for parts with simpler, symmetrical forms, complex geometries
-Uncomplicated machinery and technology, well to automation.
High-Pressure Die Casting (HPDC) is an extremely efficient manufacturing method for producing various product forms. The process forces molten metal at high speed, and high pressure into a closed steel die cavity. The die has a stationary and moving half, both of which are mounted to the die casting machine’s platens. The die casting machine has an injection end that uses hydraulics and pressurized gas to move a piston forward, injecting the molten metal into the closed steel die. The die casting machine also has a clamping end that utilizes hydraulics and mechanical toggles to absorb the injection pressure and hold the die shut while the part solidifies. The process is capable of turning molten metal into a solid near-net-shape part in seconds.
Advantages of High-Pressure Die Casting
-Fast filling, high production efficiency.
-High compactness, high product strength and surface hardness, low elongation.
-Good surface finish, generally up to RA6.3 or even Ra1.6.
-Fit for Products with thin wall thickness (the thinnest to 0.5mm).
-Much gases in Internal , poor porosity .
-Not allow heat treatment, small machining allowance (better less than 0.25mm ).
-High cost and short time life for molding
It mainly according to the wall thickness of the product:
As the high production efficiency ,the high- pressure die casting should be preferred priority if the production process and product performance can be met.
When the wall thickness of the product is over than 8mm, the high-pressure die-casting can not meet the expected requirement due to too many internal pores, the gravity die casting and low- pressure die casting can be considered.Generally ,low pressure casting is a compromise between high pressure casting and gravity casting.
TCC provide a complete manufacturing service solution for each project and application.For more information on Aluminum Gravity and Pressure Die Casting, please feel free to contact alina@tcc-casting.com.