Which welding is the better option for the defects of Aluminum alloy parts , argon arc welding (TIG/MIG), laser welding or cold welding ?
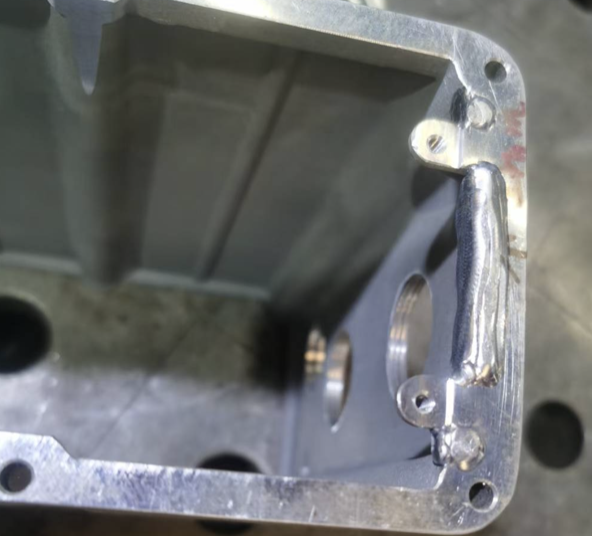
Think about the logic for selection ,
- Deformation-sensitive parts (such as machined products): cold welding → laser welding → argon arc welding
- High-strength parts : laser welding → argon arc welding → cold welding
- Thick and large parts/low-cost repair : TIG welding → Laser welding (high power)
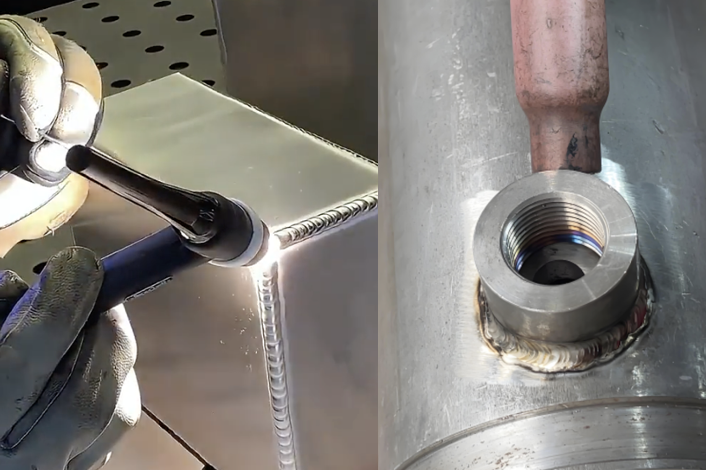
These are based on a detailed comparison of the core differences, characteristics and welding deformation of argon arc welding (TIG/MIG), laser welding and cold welding . The further specific analysis is as below :
1. Basic principles and core differences,
Method | Principle | Heat input characteristics |
TIG welding | The base metal and welding wire are melted by electric arc (non-melting electrode TIG/melting electrode MIG), and argon gas is used to protect the molten pool from oxidation. | High heat input and wide heat affected zone. |
Laser welding | The high-energy laser beam melts the metal instantly, and the argon/helium gas is used for protection, which is a high-energy density fusion welding. | Concentrated heat input and narrow heat affected zone. |
Cold welding | High-pressure plastic deformation (solid-state welding) or micro-arc discharge (micro-melting) achieves atomic-level bonding with virtually no heat generation. | Very low/no heat input , no heat affected zone. |
2.The Comparison of heat affected zone width,
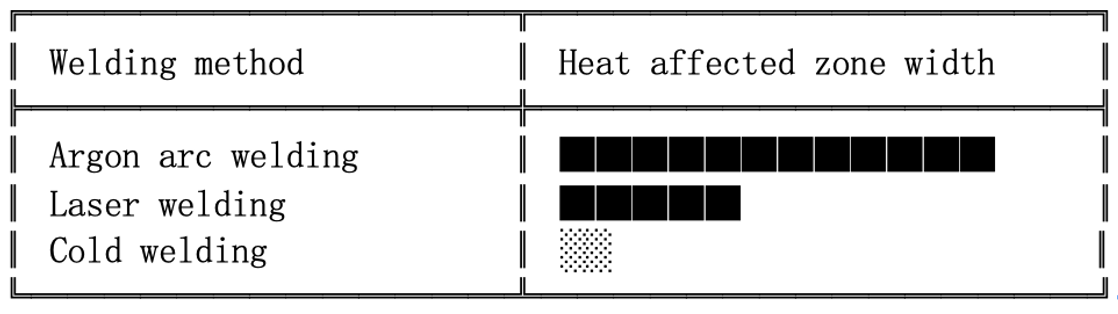
3. The Comparison of core features,
Characteristic | TIG/MIG welding | Laser welding | Cold welding |
Heat input | High, wide heat affected zone (prone to grain coarsening) | Concentrated, narrow heat-affected zone (about 1/3 of argon arc welding) | Virtually no heat input , no heat affected zone |
Welding speed | Slow (TIG) to medium (MIG) | Very fast (up to 10m/min) | Slow (spot welding/repair) |
Melt Depth | Medium-deep (current dependent) | Deep and precisely controllable (high aspect ratio) | Very shallow (surface binding only) |
Oxidation Control | Depends on the purity of argon gas. Aluminum alloy needs AC TIG to break the oxide film | Requires high-purity protective gas, sensitive to oxide film | No oxidation problems (normal temperature operation) |
Joint strength | Close to the parent material (need high-quality welding wire and process) | ≥ Parent material (deep melting welding with high density) | ≤ Parent material (joining surface is the pressing area) |
Applicable thickness | Thin-Thick (0.5mm~25mm+) | Thin-medium thick (0.2mm~12mm, high power up to 20mm) | Ultra-thin (≤2mm, repairing micro defects) |
Equipment cost | Low (TIG) / Medium (MIG) | Very high (laser + precision motion system) | Low-Medium (Press/Micro-arc Equipment) |
Technical Difficulty | Medium (TIG requires skilled workers, MIG is easy to automate) | High (needs precise parameter adjustment, centering, and protection) | Low (simple operation, mainly pressure control) |
Typical Applications | Structural parts, containers, special-shaped welds | Precision parts, battery housings, aerospace parts | Precision repair (pores, scratches), electronic components, heat-sensitive parts |
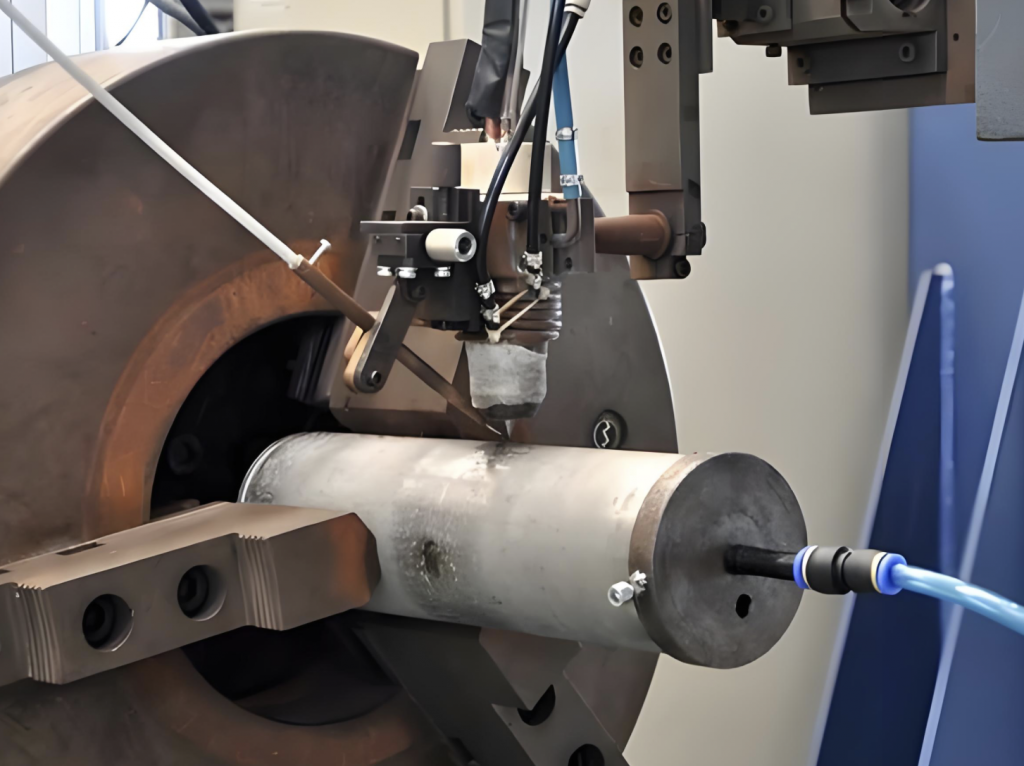
4. The Comparison of deformation after welding,
Method | Deformation Source | Deformation degree | Control Difficulty |
TIG welding | High heat input → severe thermal expansion and contraction , large residual stress, thin parts are prone to warping and corner deformation | ★★★★★ (maximum) | Thin plate deformation is difficult to control, requiring strong fixture + anti-deformation design |
Laser welding | Heat input is concentrated, but aluminum alloy conducts heat quickly → local shrinkage stress is still significant (especially in long welds) | ★★★☆☆ (Medium) | Parameter optimization can reduce deformation, but it is difficult to completely eliminate it |
Cold welding | No thermal stress , only micro plastic deformation caused by pressure | ★☆☆☆☆ (very small) | Almost no macro deformation, suitable for high-precision parts repair |

5.The key points of Deformation control,
- Argon arc welding : requires pre-setting of anti-deformation, segmented skip welding, and water-cooling tooling, and correction is often required after welding.
- Laser welding : Pulse welding, high scanning speed, and optimized path can reduce deformation, but fixtures are still required.
- Cold welding : uniform pressure is sufficient, close to “zero deformation” , and no secondary processing is required after repair.
6. Suggestions,
- Pursuing zero deformation → cold welding
▶ Applicable scenarios: repair of precision instrument parts, thin-walled parts (≤2mm), heat-treated parts, electronic housings.
▶ Limitations: low strength requirements (≤80% of parent material), limited to small area repairs. - Balance strength and deformation → Laser welding
▶ Applicable scenarios: aerospace parts, sealed housings, battery welding (deep melting requirements), automated production lines.
▶ Key: High equipment investment, suitable for mass production. - Cost priority, accept controllable deformation → TIG welding
▶ Applicable scenarios: large structural parts, thick plates (>5mm), non-standard single-piece production.
▶ Skills: TIG is used for high-quality welds, MIG improves efficiency; the surface of the welding material needs to be strictly cleaned.
Conclusion,
Dimensions | TIG welding | Laser welding | Cold welding |
Heat input | high | Medium-High (Concentrated) | none |
Deformation | great | medium | Very small |
strength | High (close to base material) | Very high (deep melting and dense) | Medium-Low |
cost | Low | Very high | middle |
Best Scenes | Thick plates, structural parts | Precision parts, deep melting requirements | Ultra-thin parts, zero deformation repair |
The influence of material properties on welding repair selection
The different materials of aluminum alloy have significant differences in adaptability to welding repair methods due to differences in alloying elements, heat treatment characteristics, etc.,
Material Category | Feature | Optimal welding method |
6xxx series ( Al-Mg-Si ) | Heat treatment strengthened type, difficult to restore mechanical properties after welding | Laser welding / cold welding (low heat input) |
5xxx series (Al-Mg ) | Non-heat treatment strengthening, stable performance after welding | High suitability for MIG/ cold welding |
2xxx series (Al-Cu ) | High crack sensitivity, difficult welding | Laser welding requires preheating + post-heating |
7xxx series (Al-Zn-Mg ) | High strength, easy to soften | Cold welding is suitable for small area repairs, laser welding should be used with caution |
Post-weld heat treatment/correction needs assessment
The impact of different welding methods on subsequent processes is as follows,
Welding method | Need heat treatment after welding? | Need Shaping calibration? | Precautions |
TIG welding | T6 state is required , reheat treatment is recommended | Need (especially thin parts ) | Easy to warp |
Laser welding | Small thermal impact, generally no need | May need | High automation precision but high equipment cost |
Cold welding | No | No | Fine repair is suitable, and structural parts are used with caution |